Motors and controllers
Laboratory
Motors and controllers Laboratory
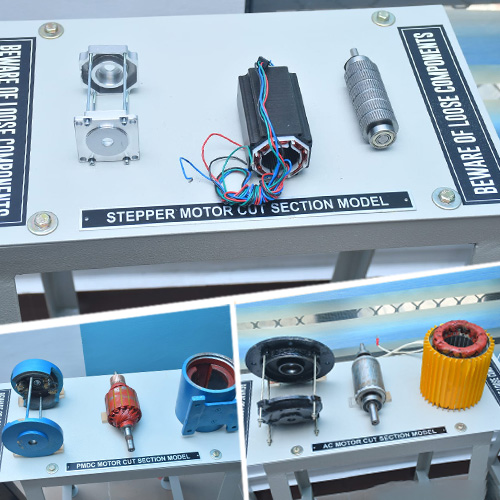
Cut Section Analysis of AC and DC Motors
Our lab is equipped for an in-depth examination and analysis of various motor types, including DC, Stepper, BLDC (Brushless DC), PMSM (Permanent Magnet Synchronous Motor), and SRM (Switched Reluctance Motor). This state-of-the-art facility allows for a comprehensive study of internal motor components and structures.
We explore how electromagnetic fields are generated within motors and how they interact with different components, shedding light on essential electromagnetic principles
Our analysis includes identifying areas within the motor that may be susceptible to wear, stress, or failure, providing insights into maintenance and longevity.
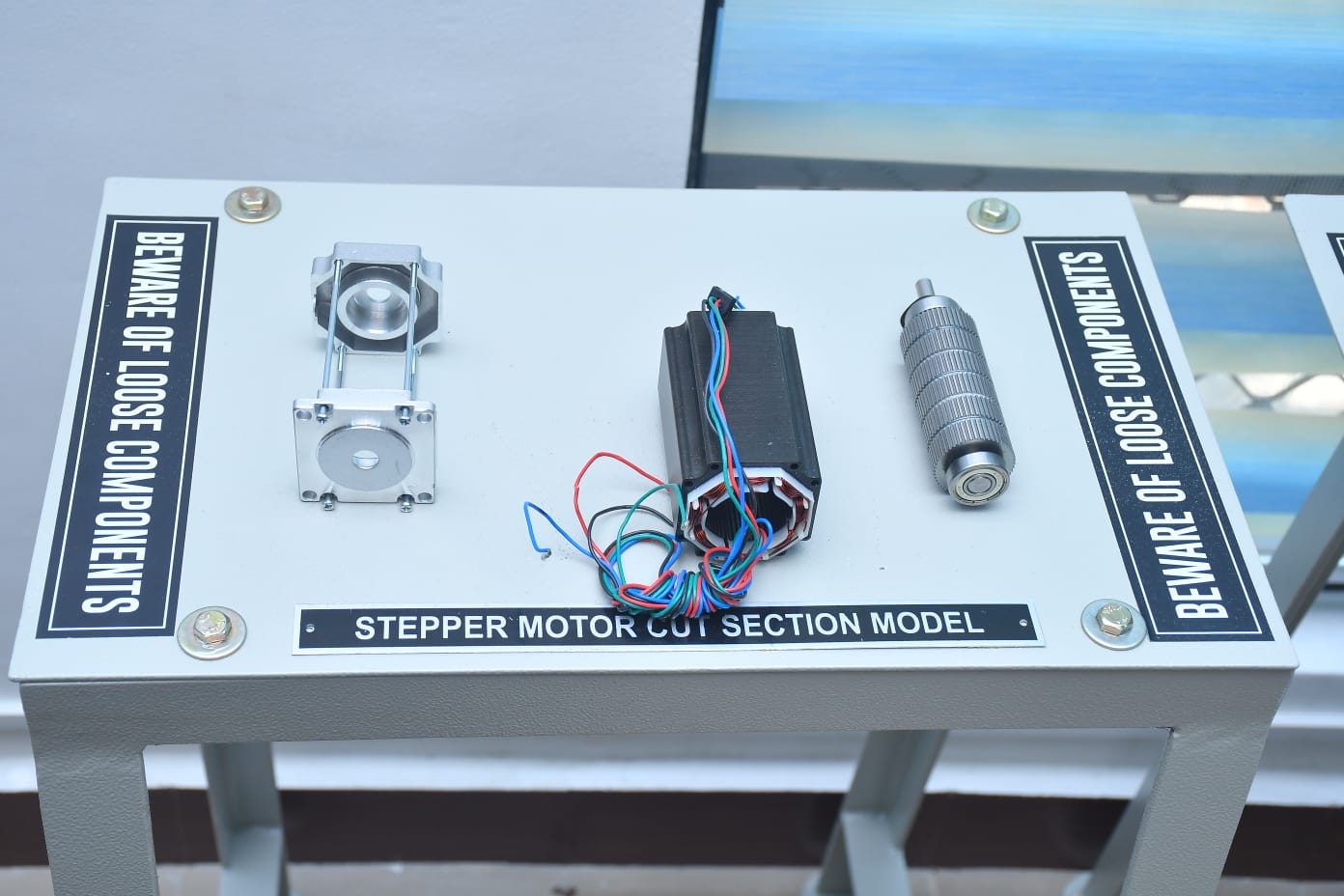
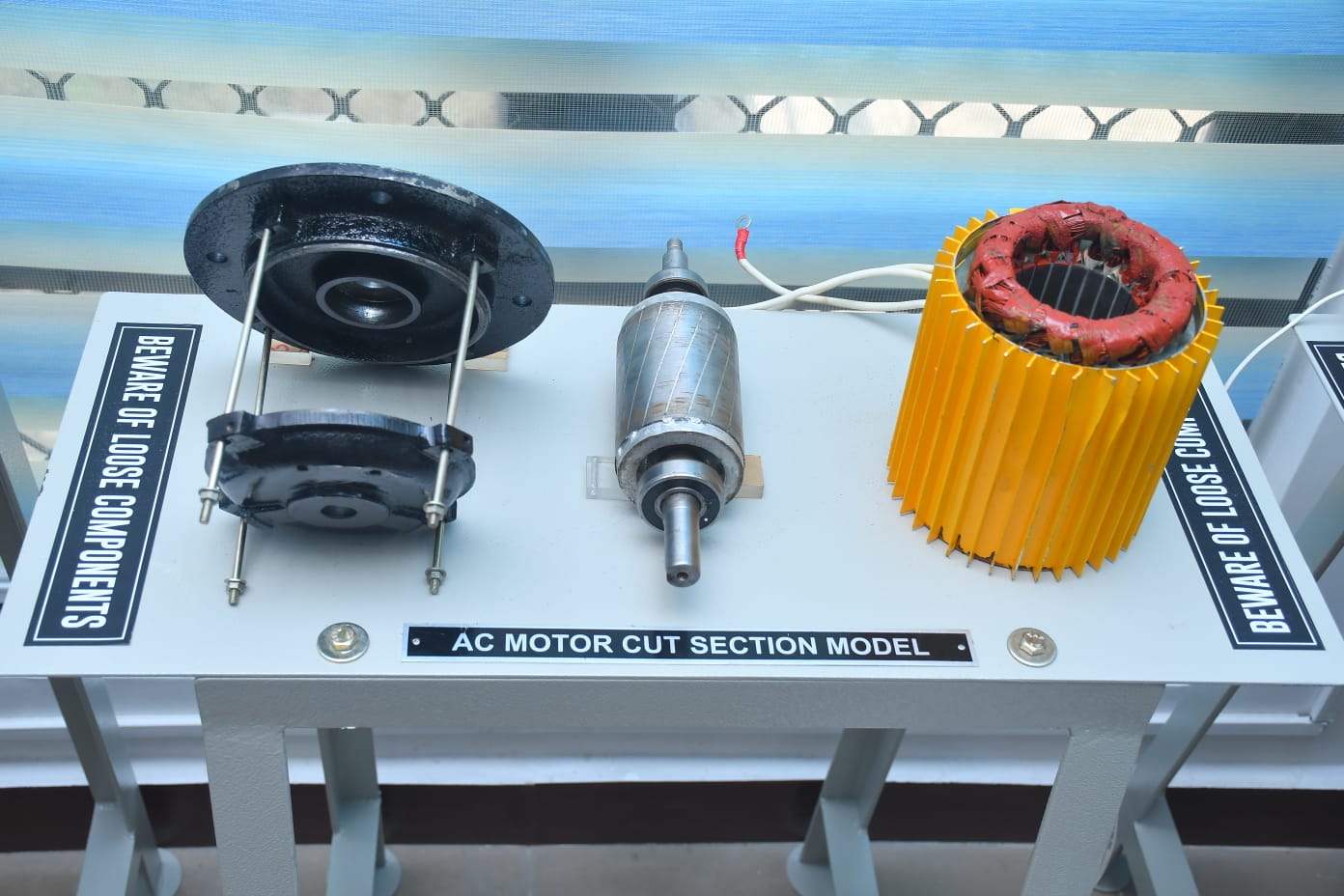
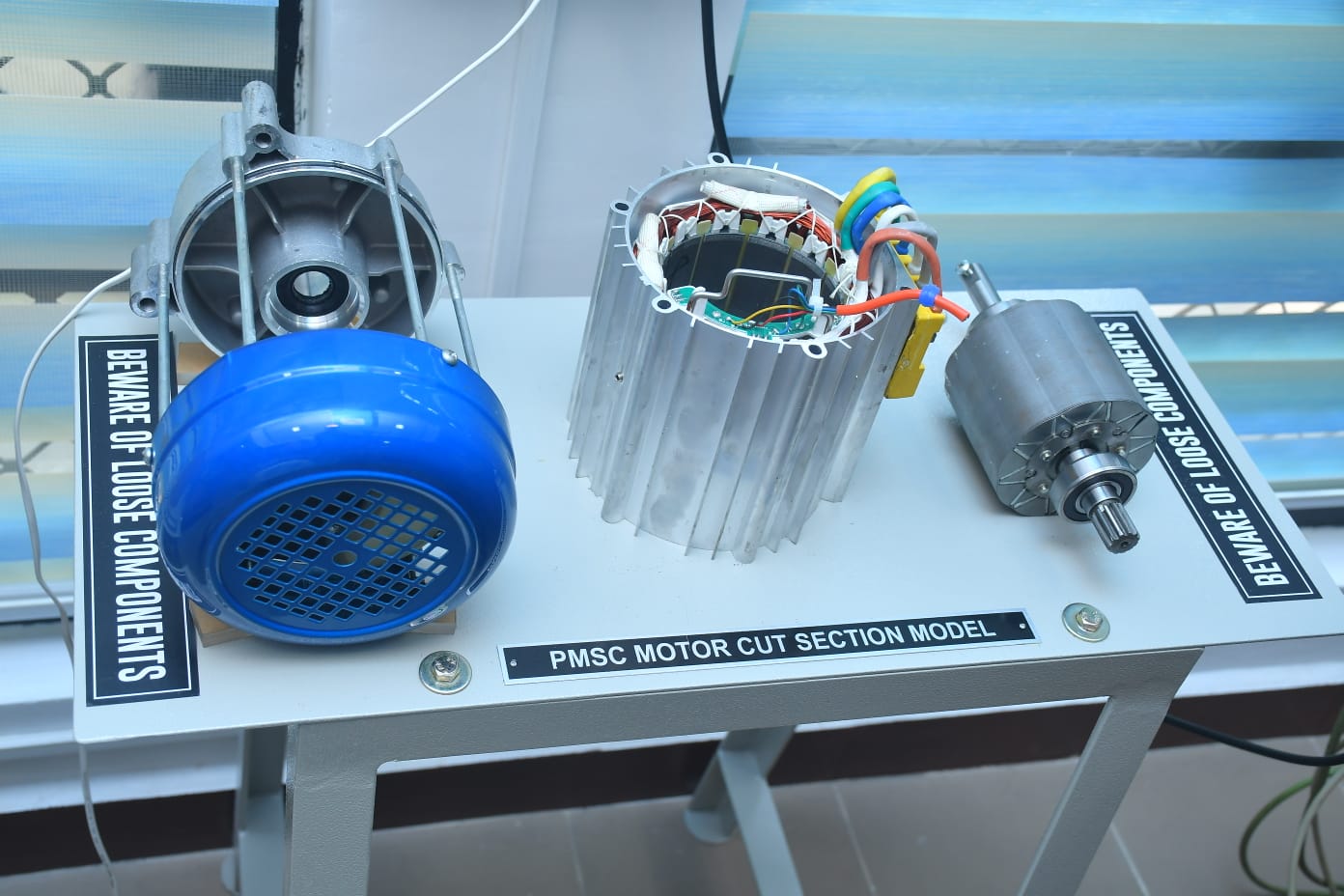
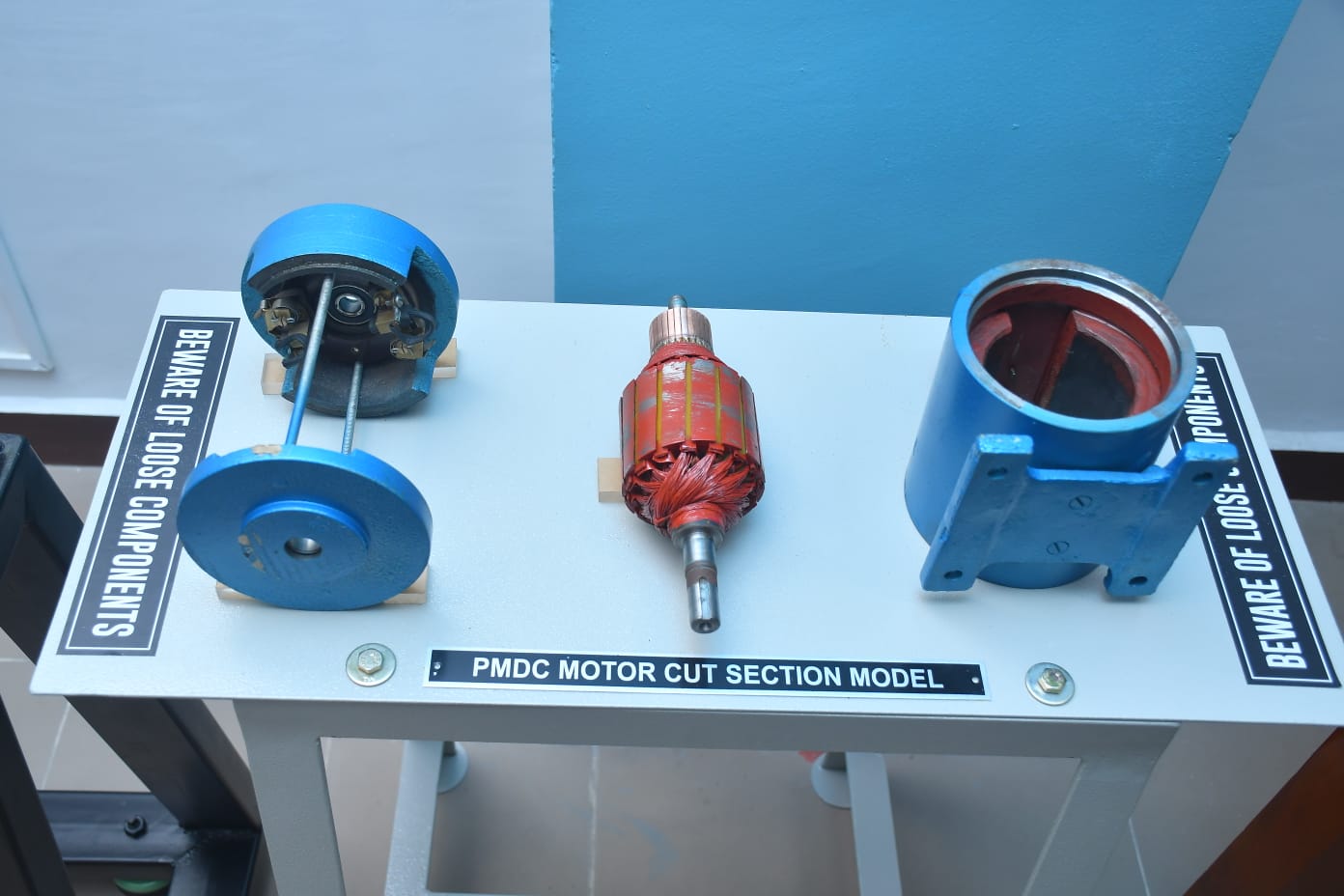
Speed Control & Drive Characteristics of Differentially Mounted PMSM/SRM Motors Using EV Power Train Control Panel
Our control panel includes advanced measurement tools for:
- Voltage Measurement: Monitor voltage levels to ensure optimal operation and efficiency.
- Current Measurement: Assess current draw to evaluate motor performance and identify potential issues.
- Motor Speed Measurement: Accurately measure motor speed to analyze response and control strategies.
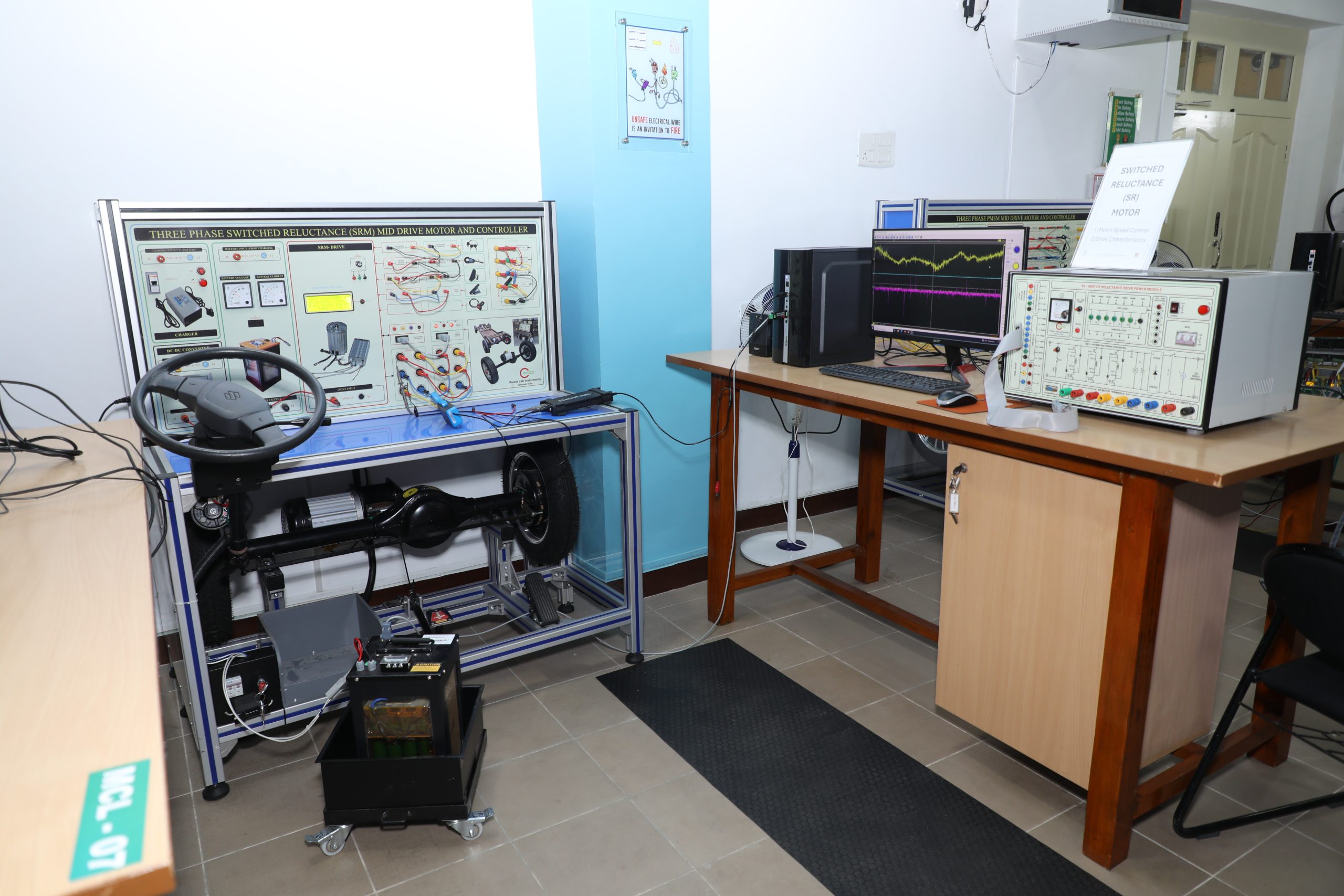
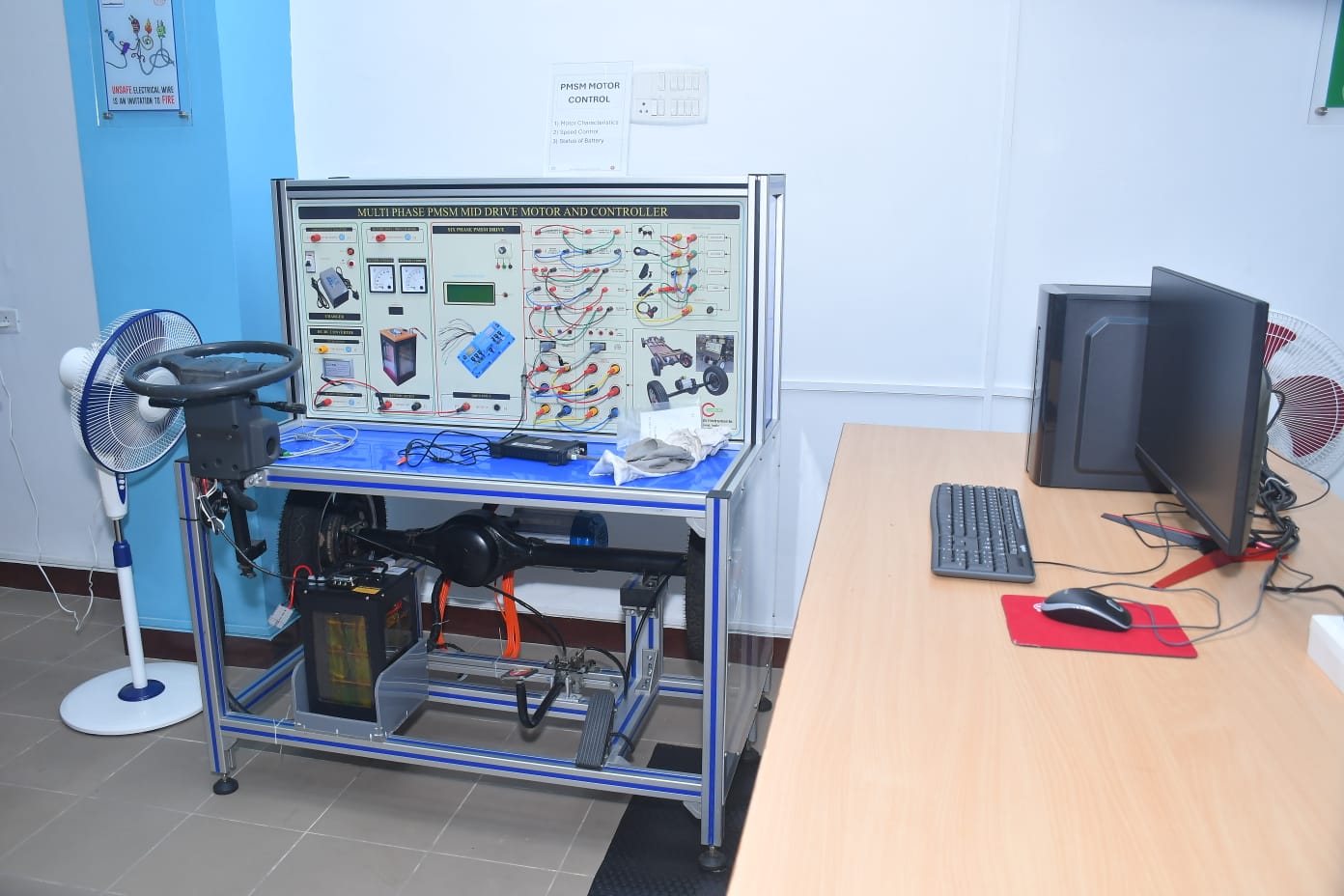
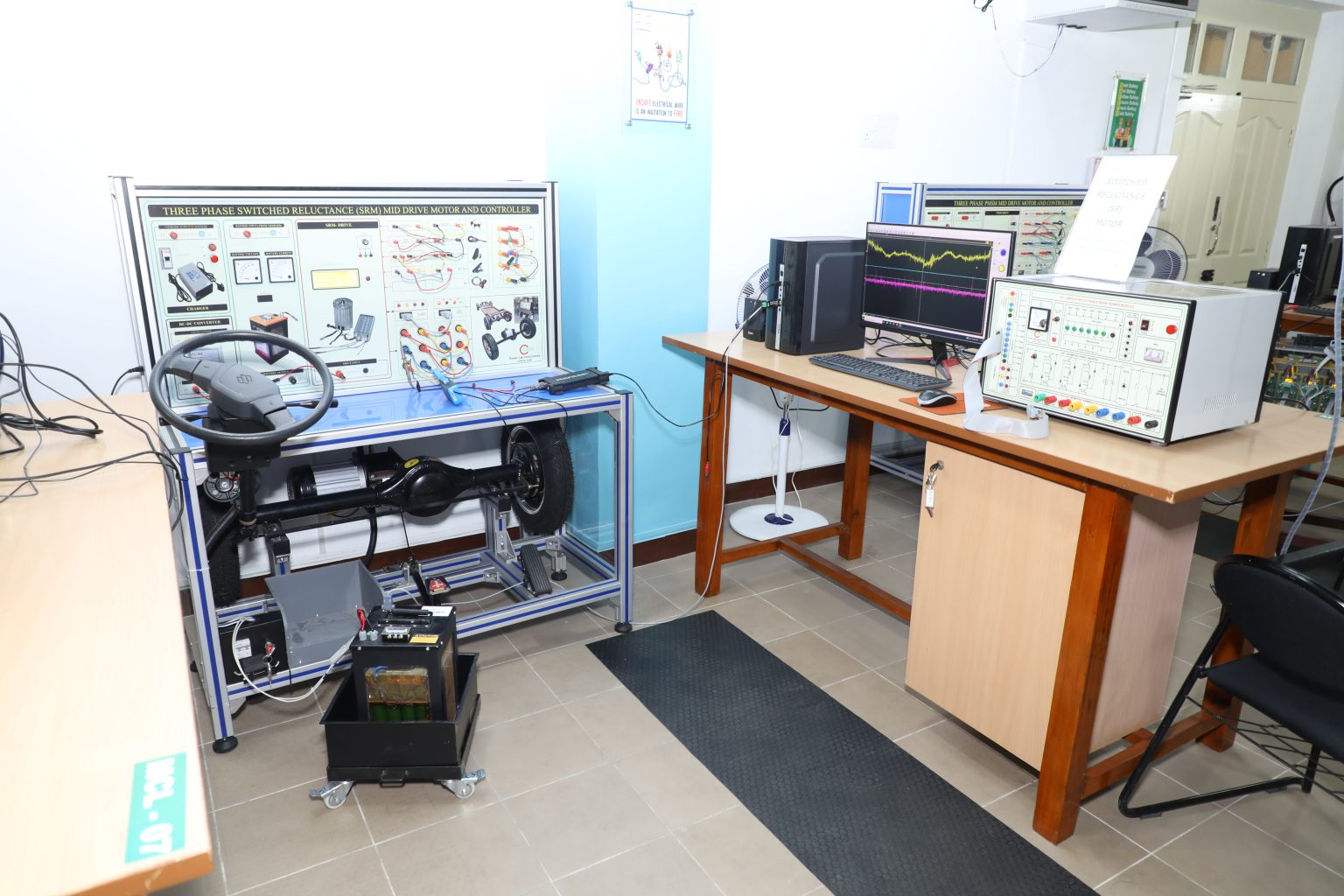
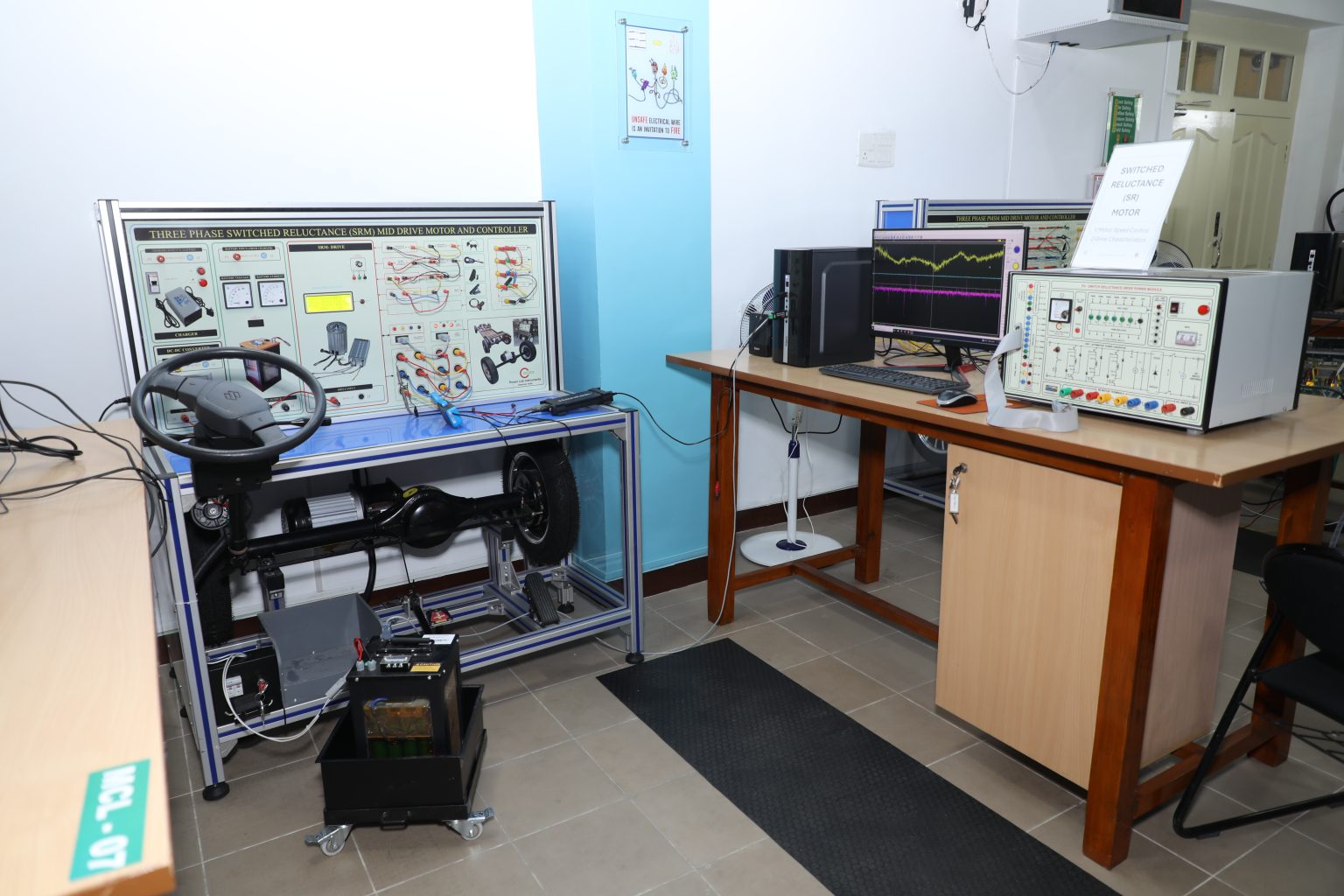
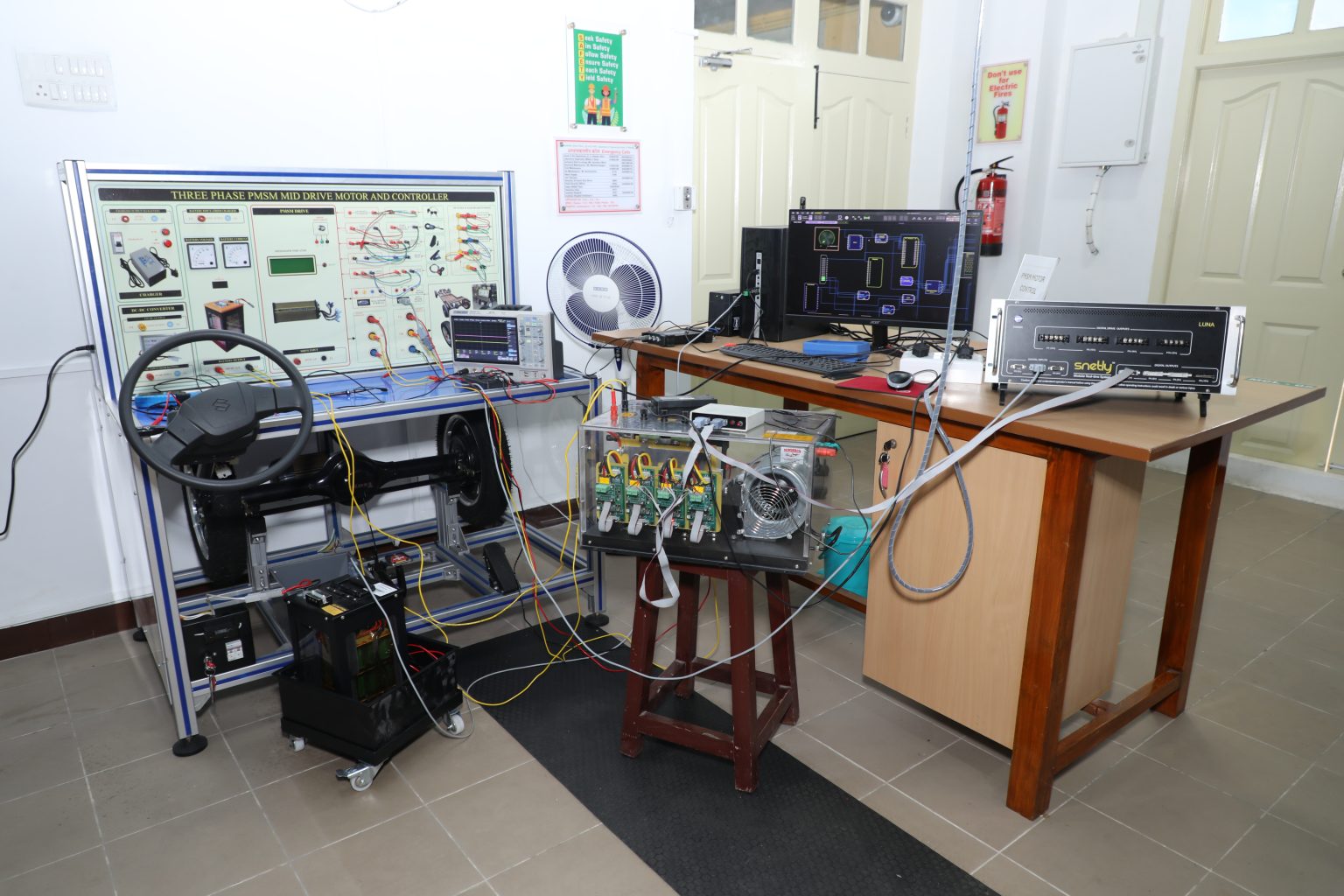
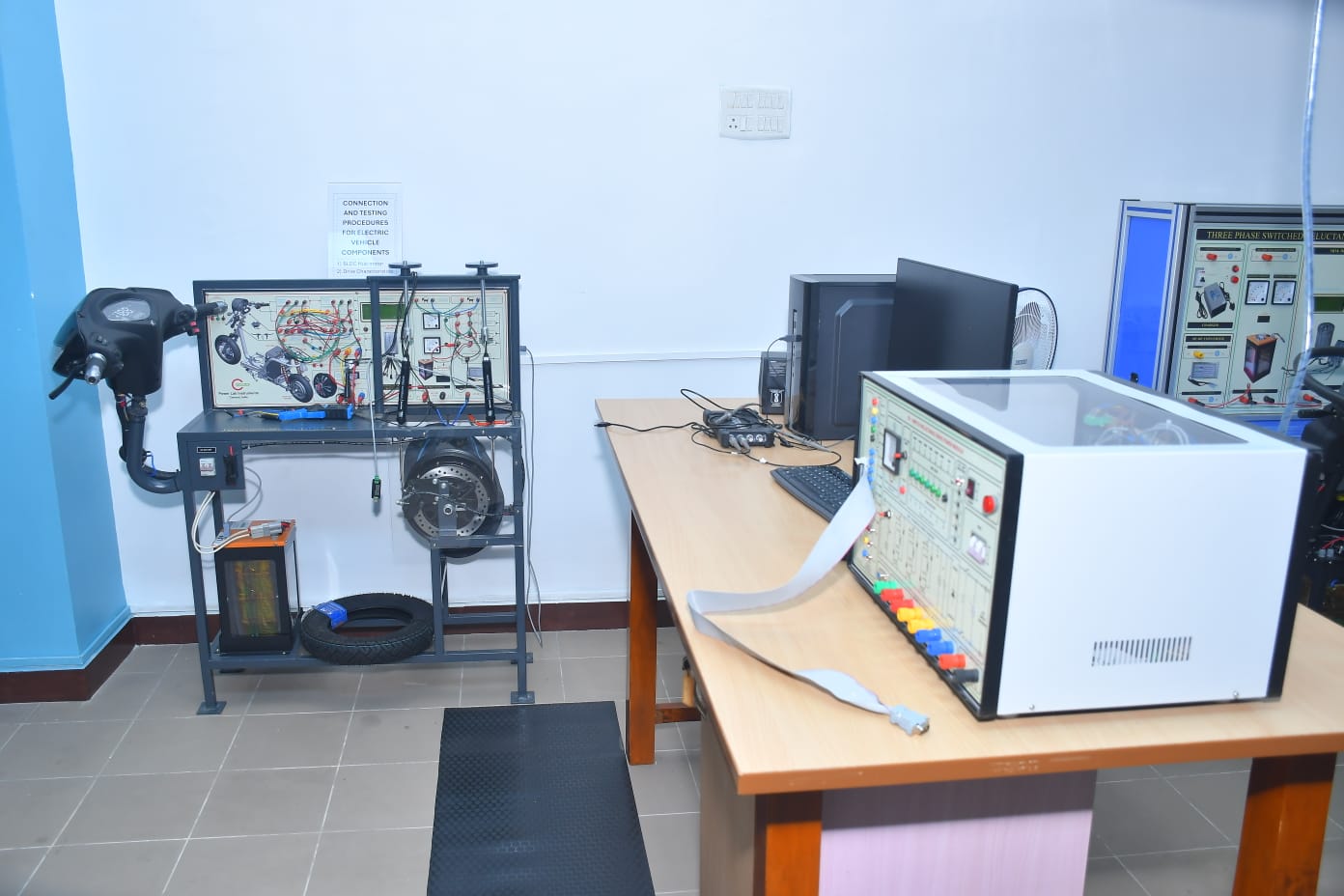
Speed Control, Torque & Drive Characteristics of In-Wheel (Hub) BLDC Motors Using EV Power Train Control Panel
Our lab is equipped with a setup for analyzing the speed control, torque, and drive characteristics of in-wheel (hub) Brushless DC (BLDC) motors within electric vehicle (EV) powertrains. This facility is essential for understanding the dynamics of modern two-wheeler electric vehicles.
Explore the critical components of two-wheeler EV powertrains, gaining insights into how each part works together to deliver optimal performance and efficiency.
- Voltage Measurement: Monitor voltage levels to ensure efficient operation and diagnose potential issues.
- Current Measurement: Analyze current consumption to assess motor performance and power distribution.
- BLDC Motor Speed Measurement: Accurately measure the speed of BLDC motors to evaluate control strategies and responsiveness.
Gain a thorough understanding of the Battery Management System, including its role in monitoring battery health, state of charge, and ensuring safe and efficient operation of the electric powertrain.
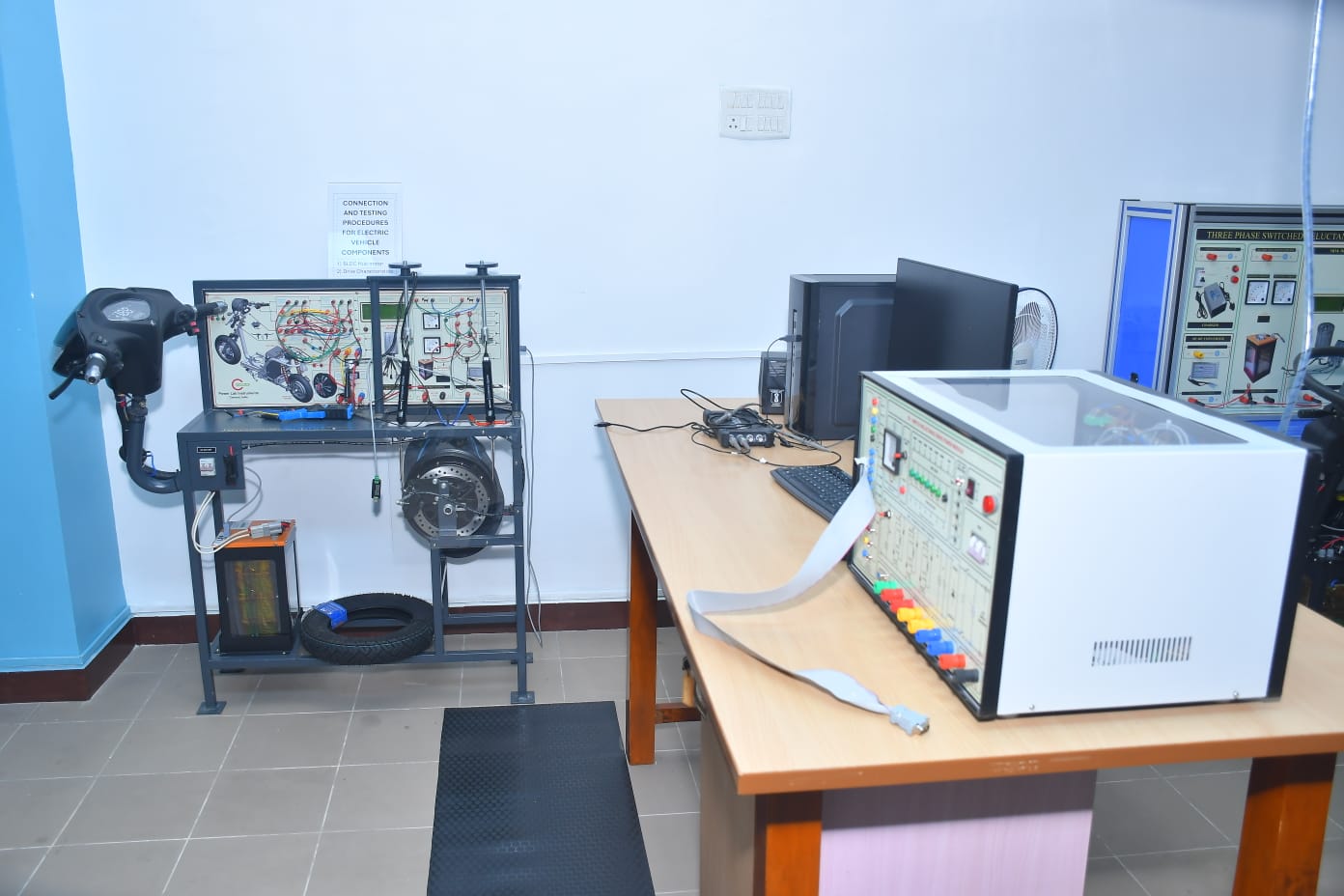
Torque Measurements Using MAGTROLL DSP6001 Tandem Dynamometer
Our lab is equipped with the MAGTROLL DSP6001 Tandem Dynamometer, a state-of-the-art device designed for precise torque measurements in various motors. This equipment is essential for researchers and engineers looking to evaluate motor performance under diverse conditions.
The dynamometer allows for accurate measurement of speed, torque, and power output of motors, providing essential data for performance analysis.
Analyze the dynamic torque response of the motor under test, including its behavior during transient conditions. This feature is critical for understanding how motors react to sudden changes in load or speed.
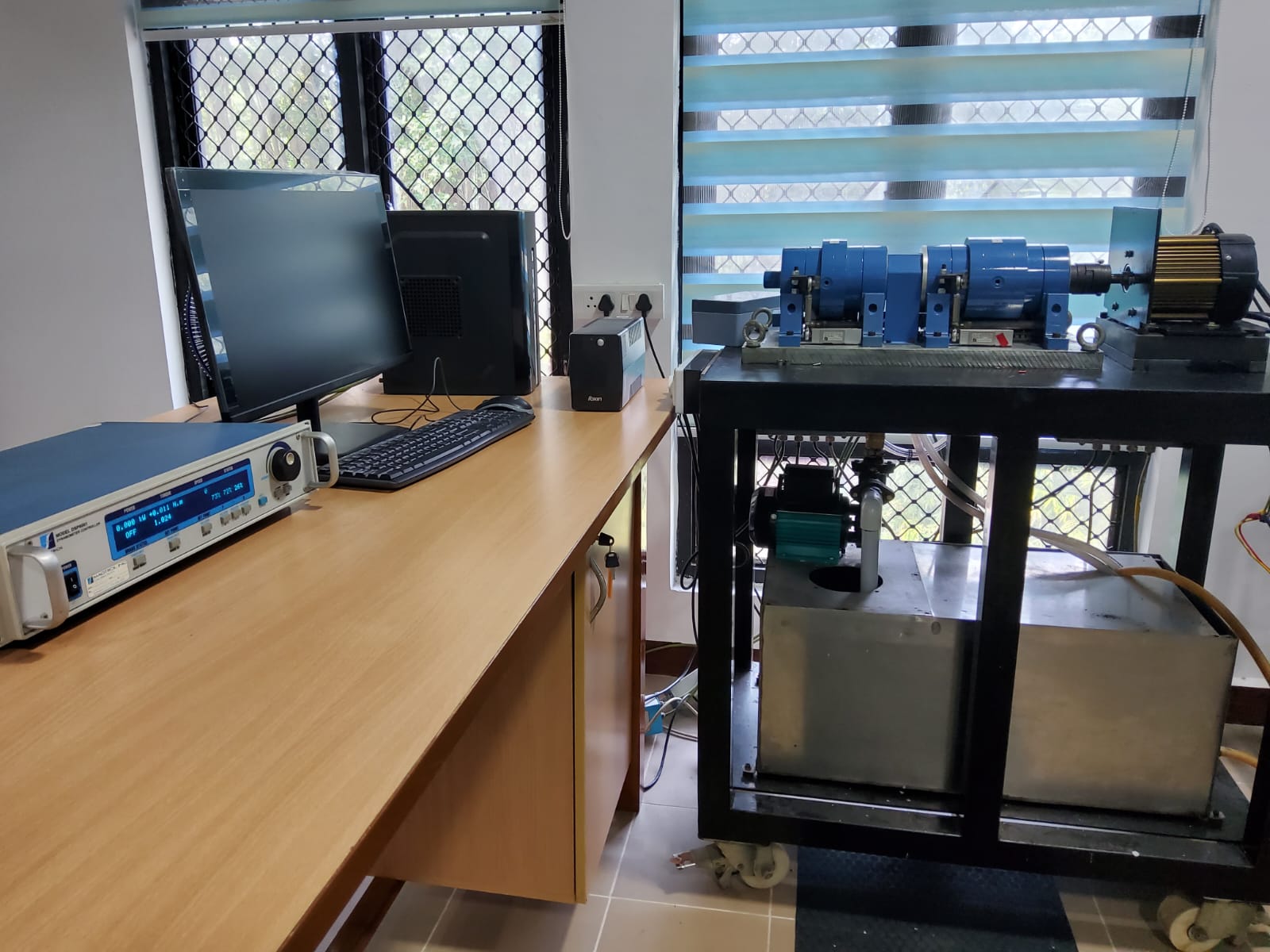
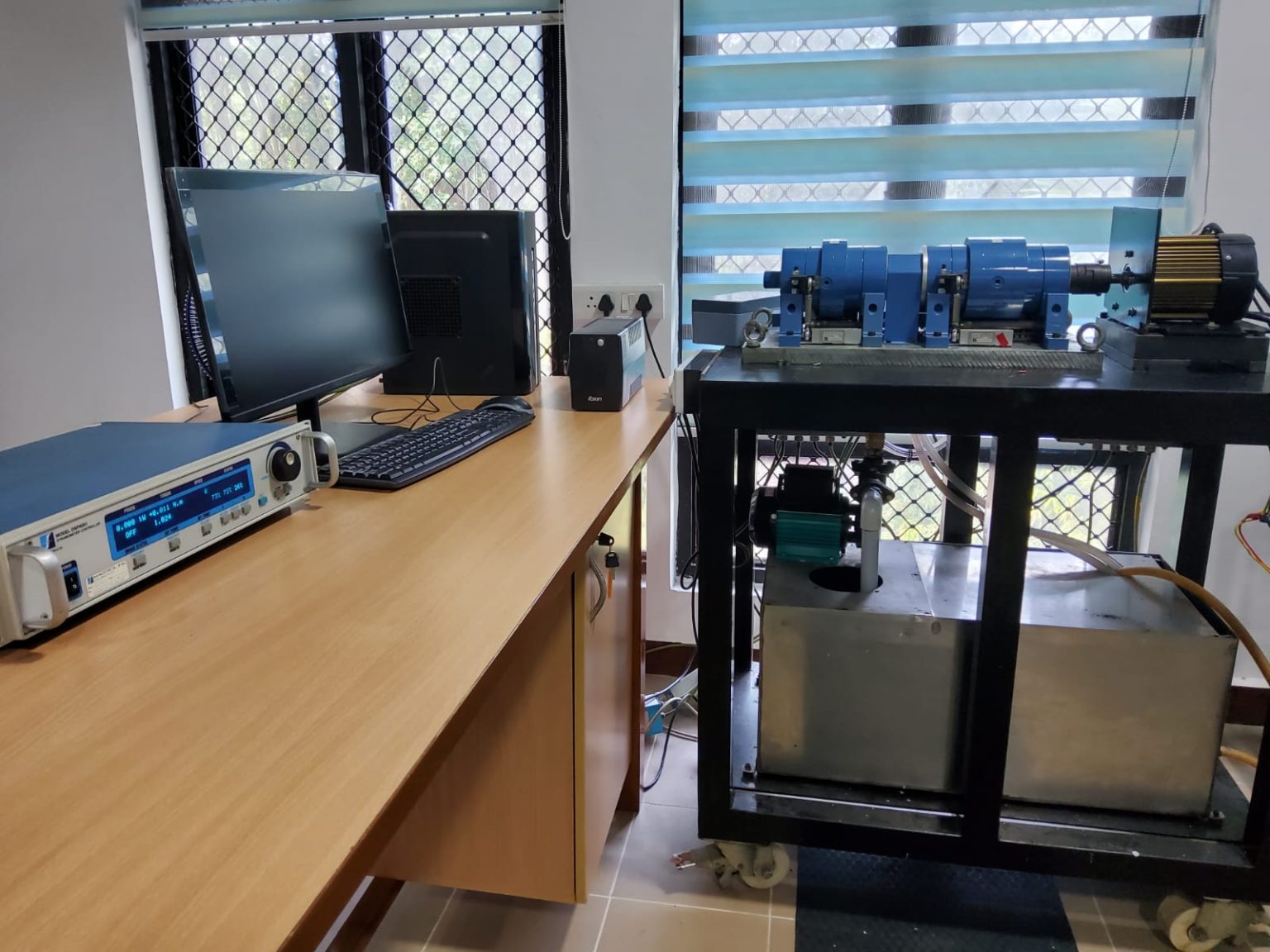
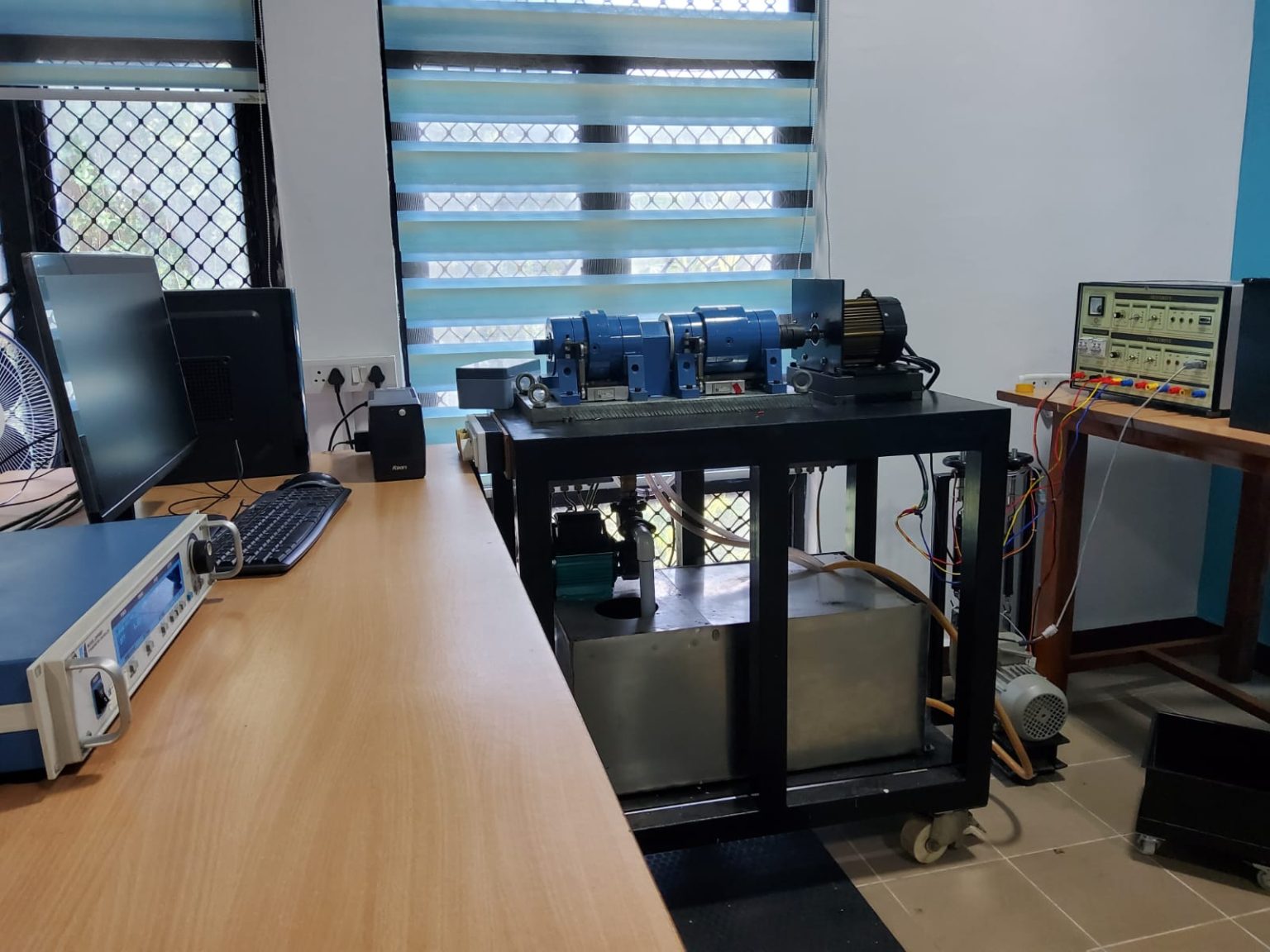
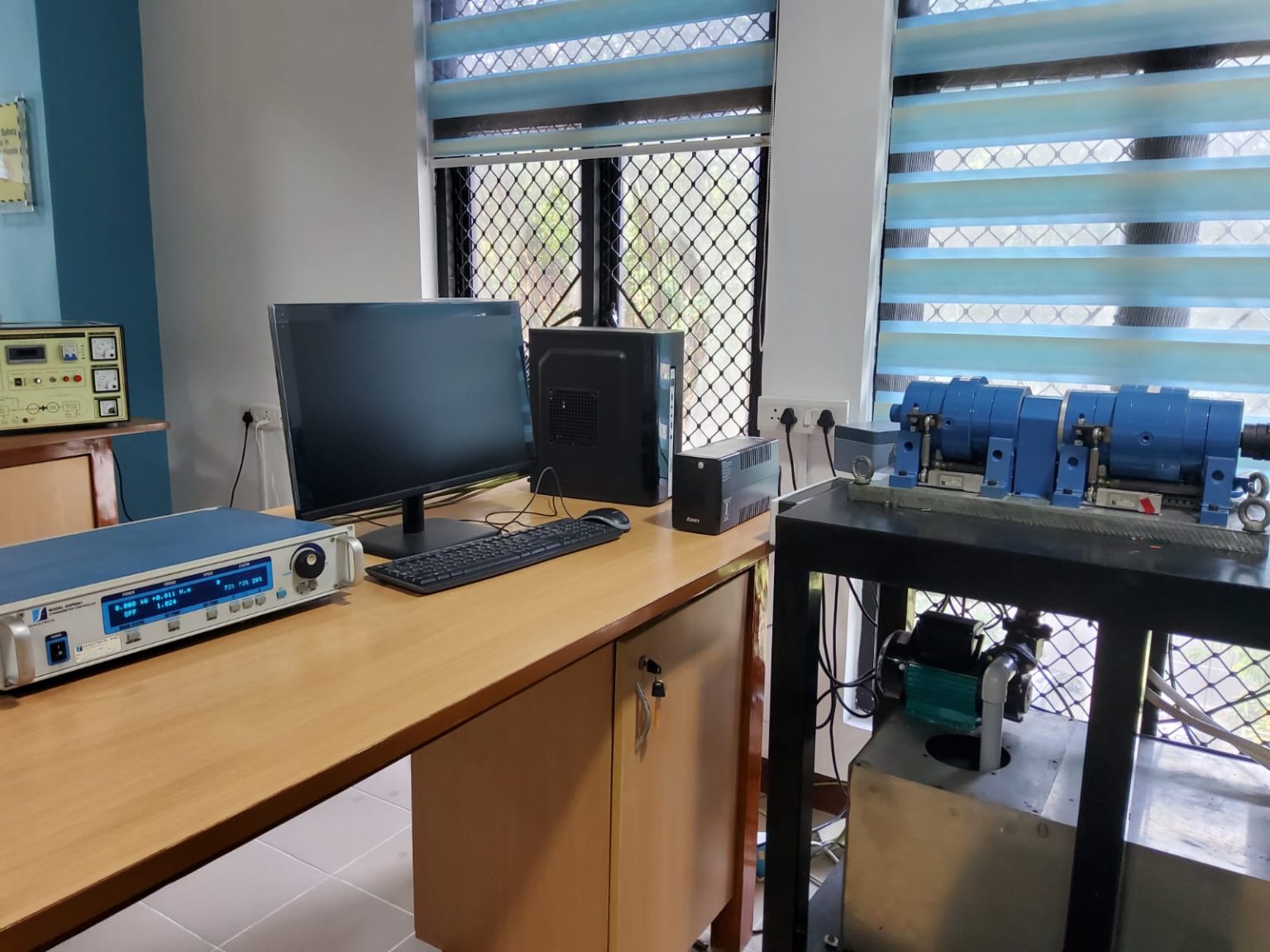
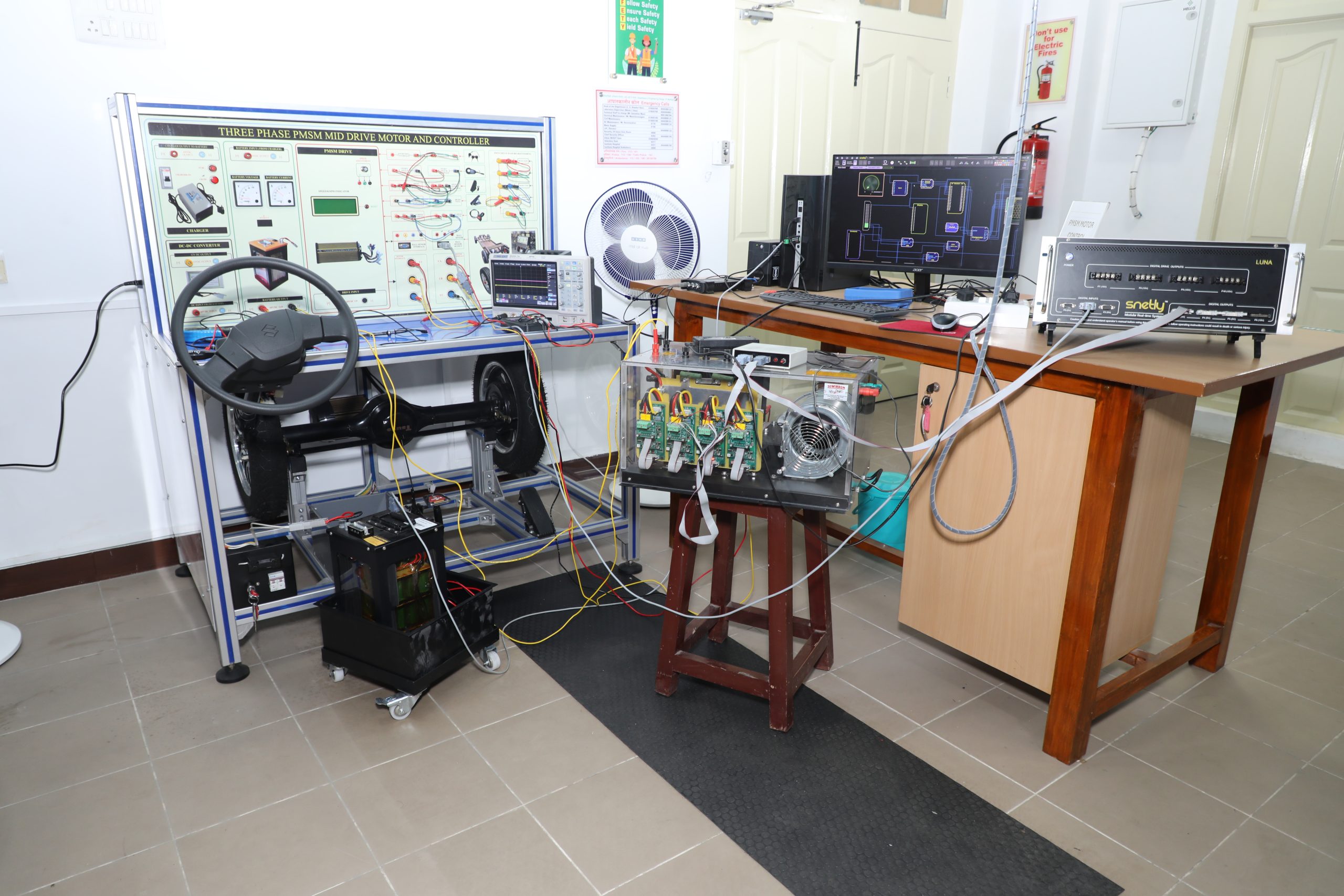
Control Strategy of Electric Motors Using Snetly FPGA
Our lab is equipped to develop and implement advanced control strategies for various electric motors, including Brushless DC (BLDC), Switched Reluctance (SR), Permanent Magnet Synchronous Motors (PMSM), and Induction Motors. Utilizing the Snetly FPGA (Field Programmable Gate Array), we enable real-time control algorithms that enhance motor performance and efficiency.
Design and implement sophisticated control algorithms tailored for different motor types. This capability allows for precise control of motor behavior in real-time applications.
Our setup supports a range of electric motors, including BLDC, SR, PMSM, and Induction Motors, providing flexibility in research and experimentation.
Leverage the power of Snetly FPGA to achieve high-speed processing and responsiveness in motor control. This technology enables the execution of complex algorithms with minimal latency.
Experiment with various control strategies to optimize motor performance, efficiency, and response under different operational conditions.
This equipment is essential for researchers and engineers focused on motor control technologies, enabling innovative solutions for electric drive systems across diverse applications.
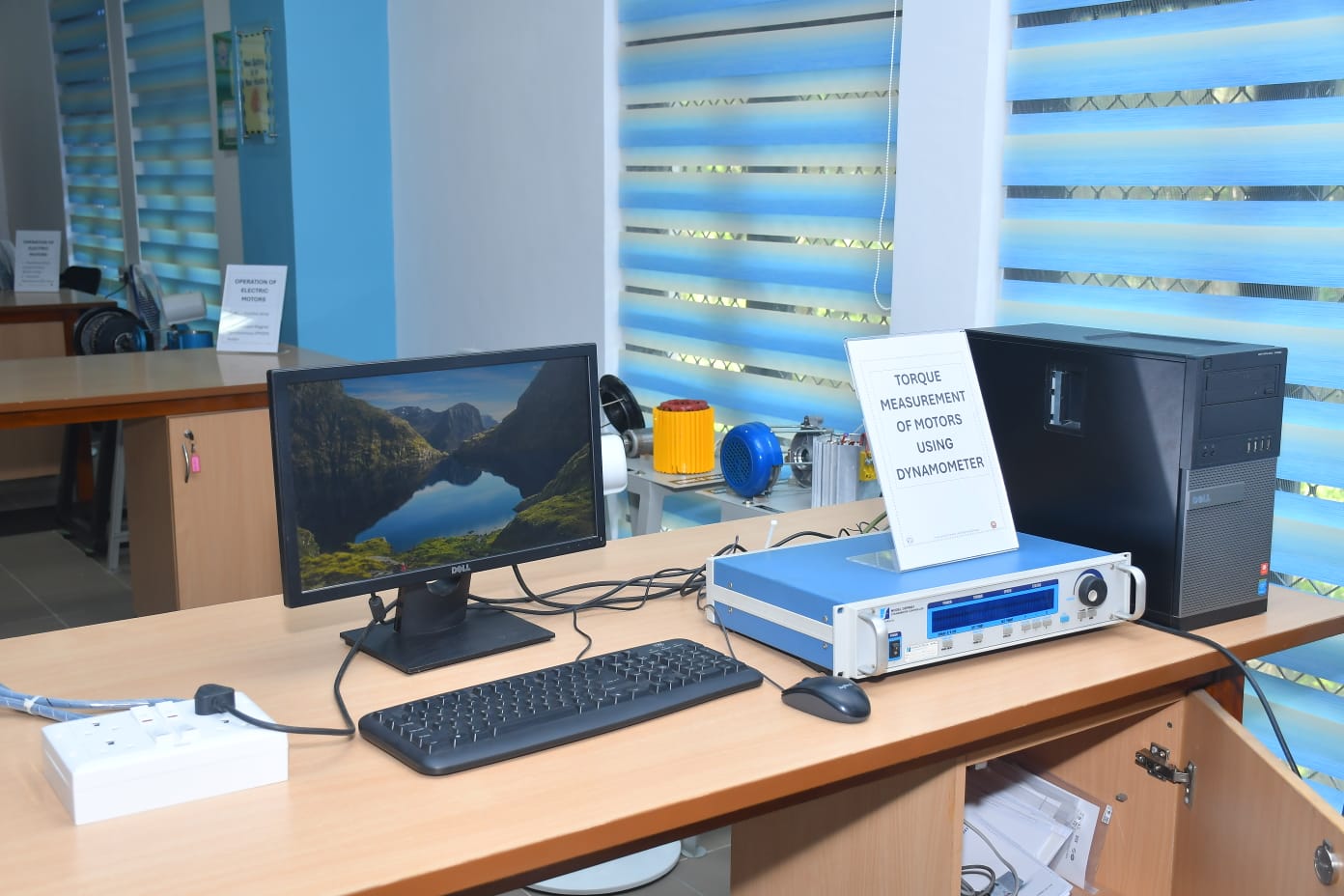
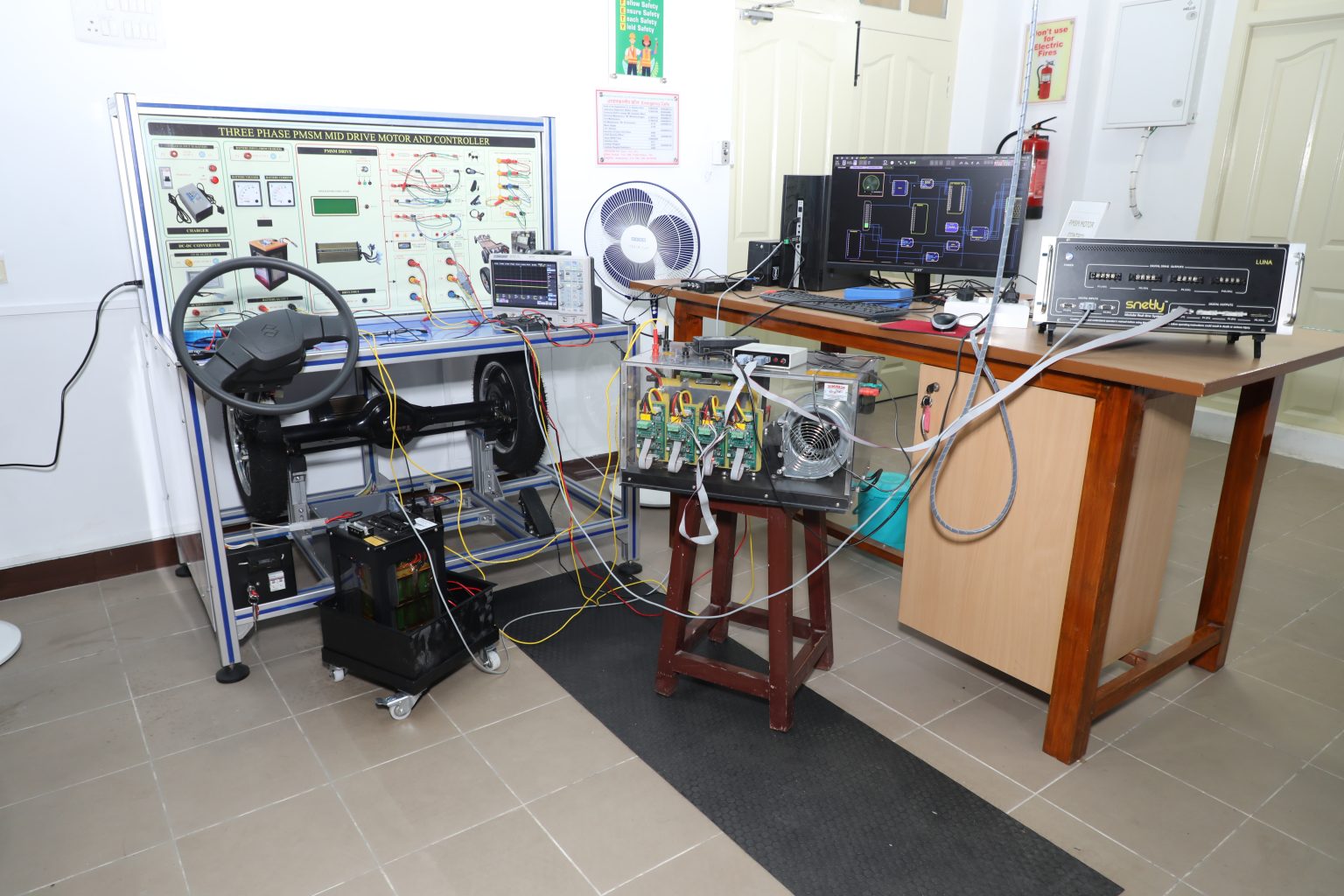
Study of Regenerative Braking System
Our lab is equipped to conduct in-depth studies on regenerative braking systems, an essential technology for enhancing energy efficiency in electric and hybrid vehicles. This facility enables users to explore the principles and practical applications of regenerative braking.
Gain a comprehensive understanding of the fundamental principles and mechanisms that underpin regenerative braking systems. This includes studying how kinetic energy is converted back into electrical energy during braking.
Conduct experiments to simulate various braking scenarios and downhill driving conditions. This allows for a thorough investigation of system behaviour and efficiency.
Measure the voltage and current generated during regenerative braking under controlled conditions. This data is crucial for assessing the effectiveness of the braking system and its impact on overall vehicle performance.
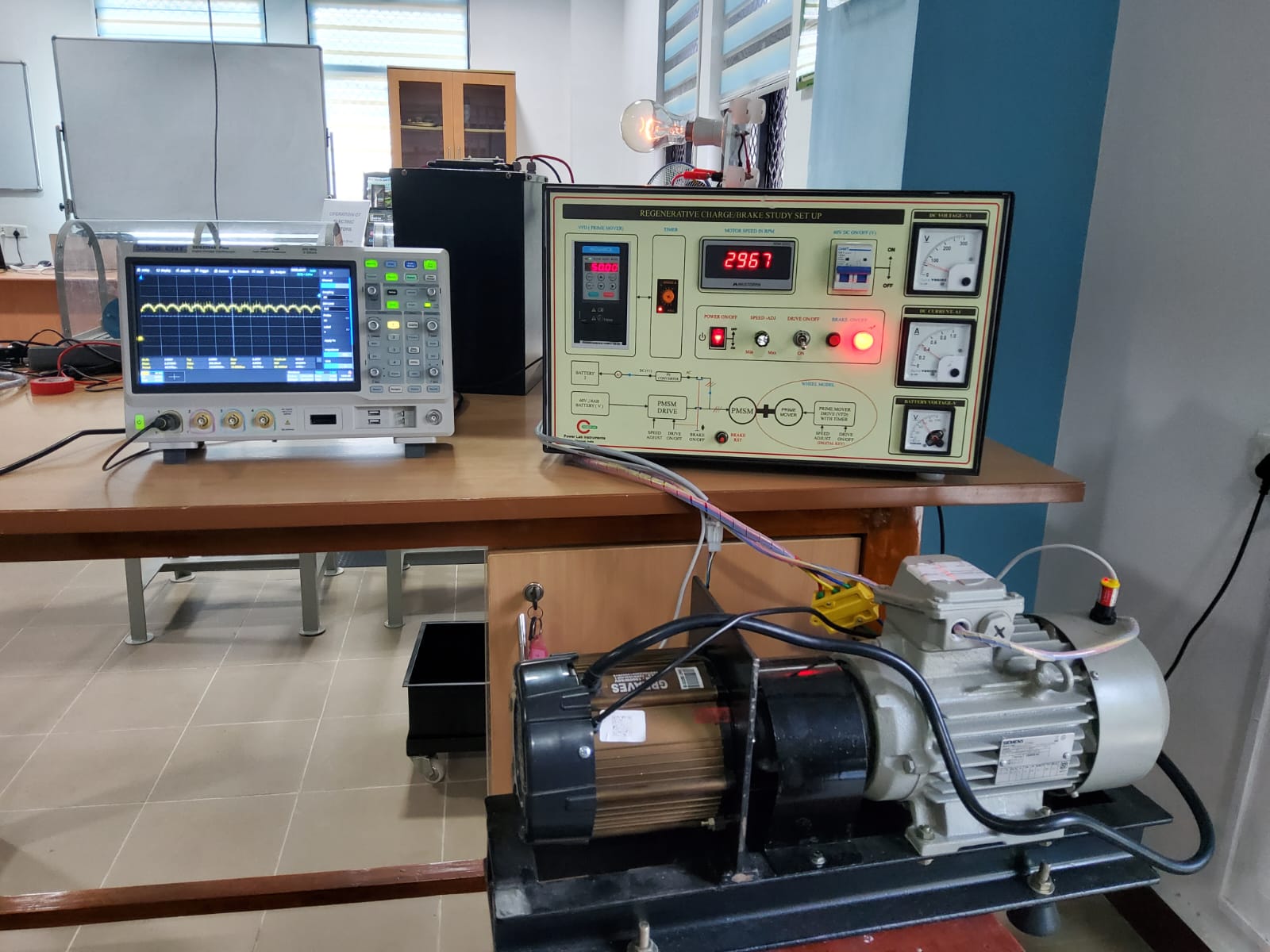
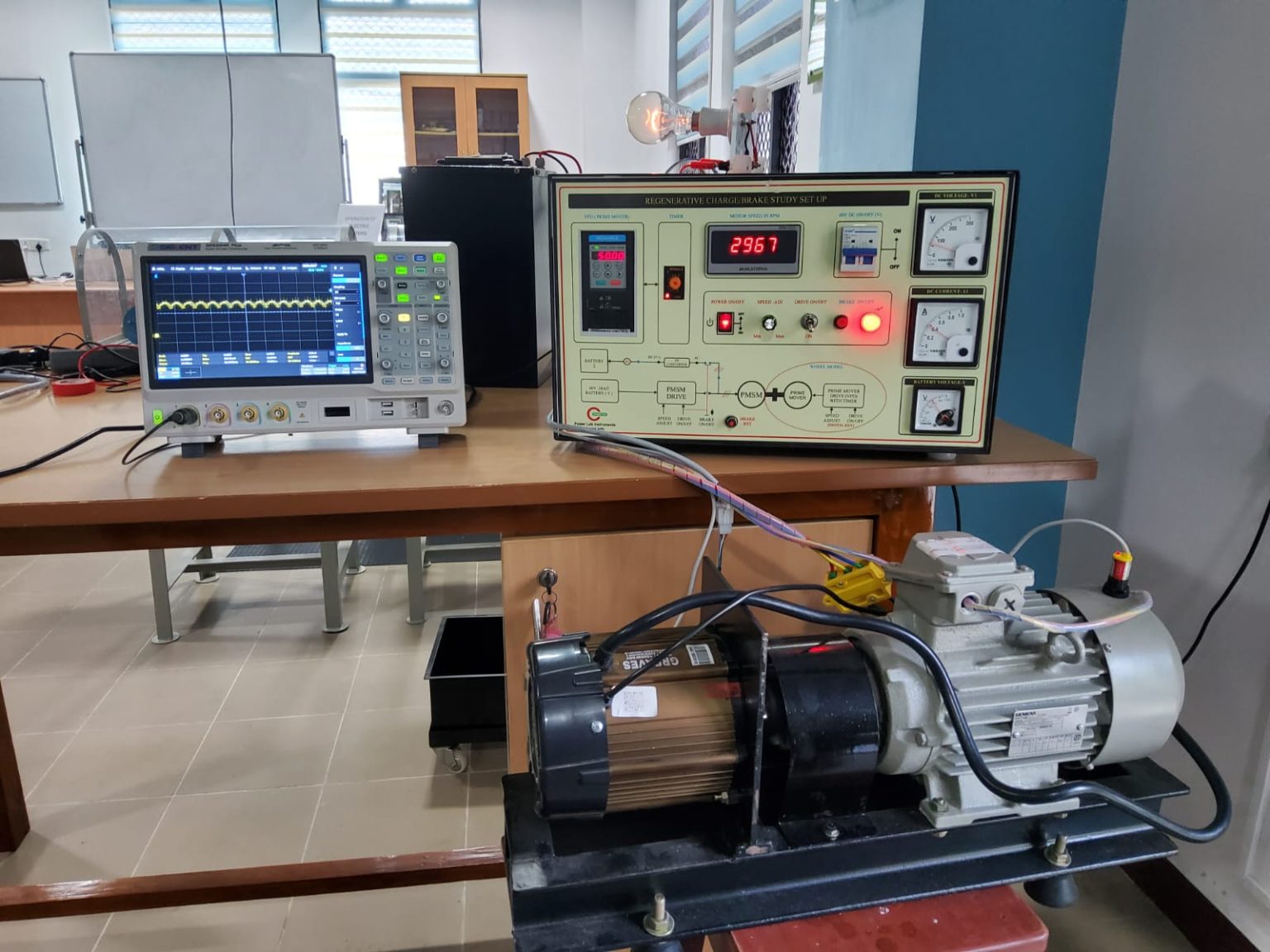
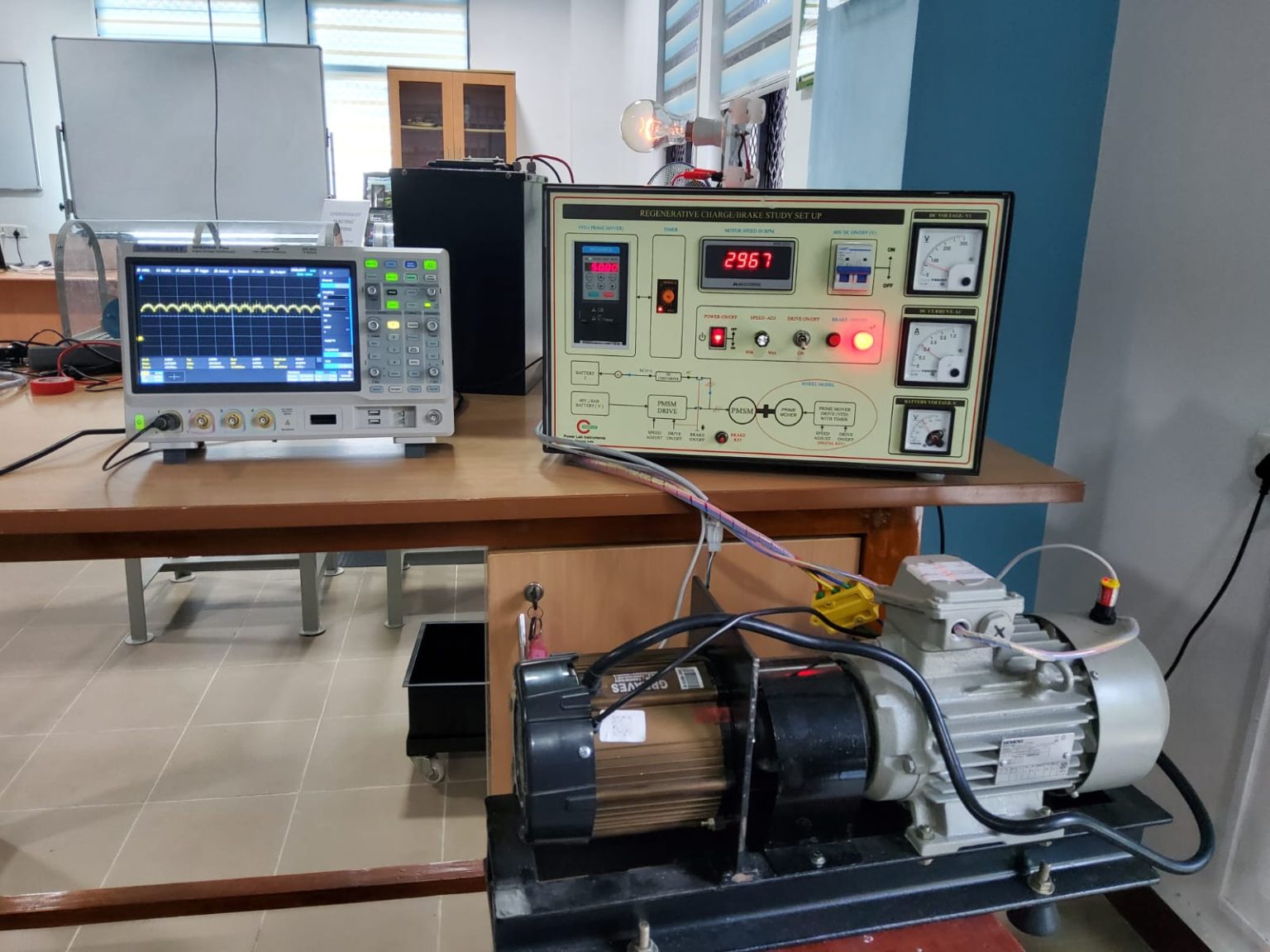
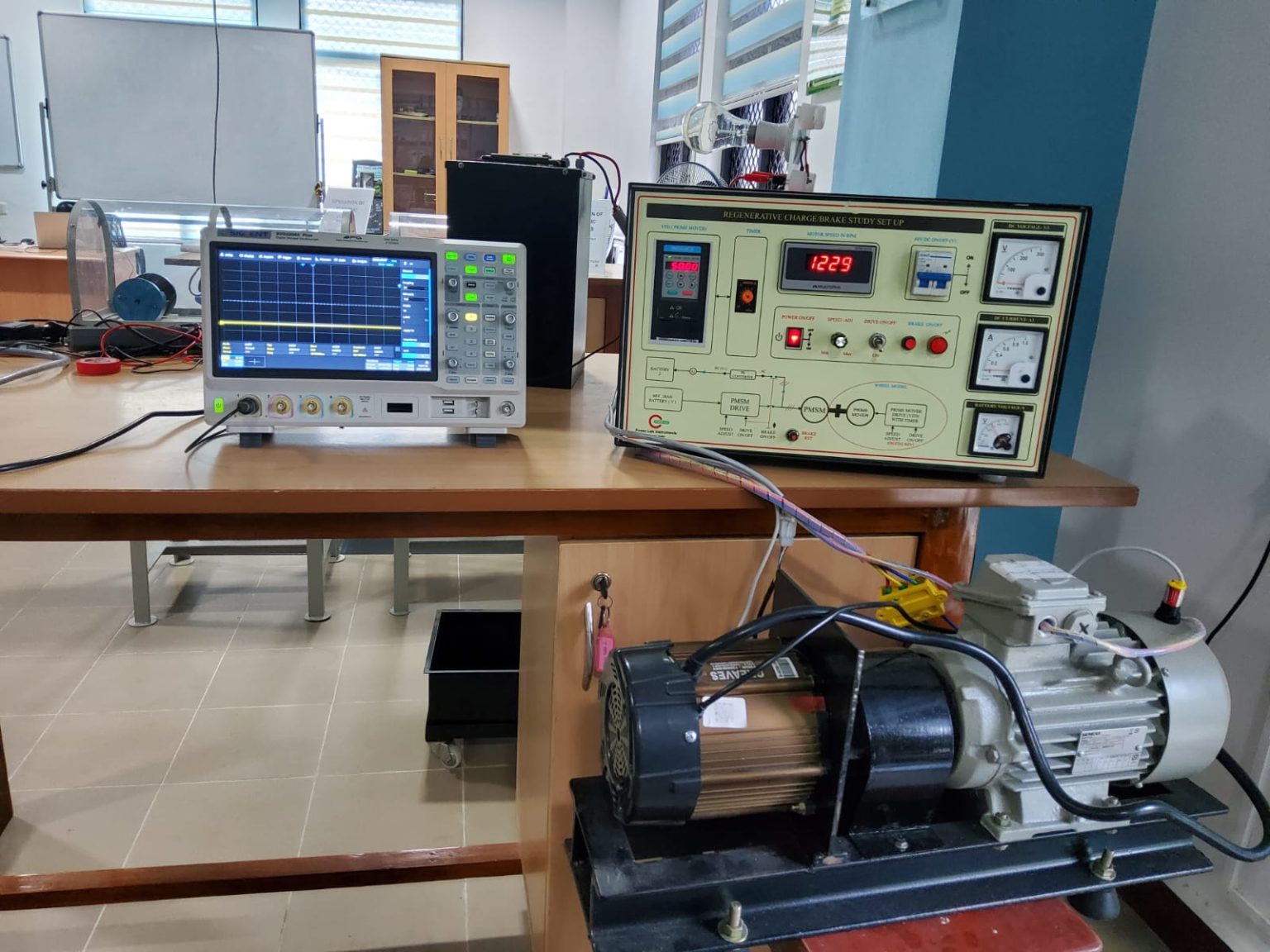
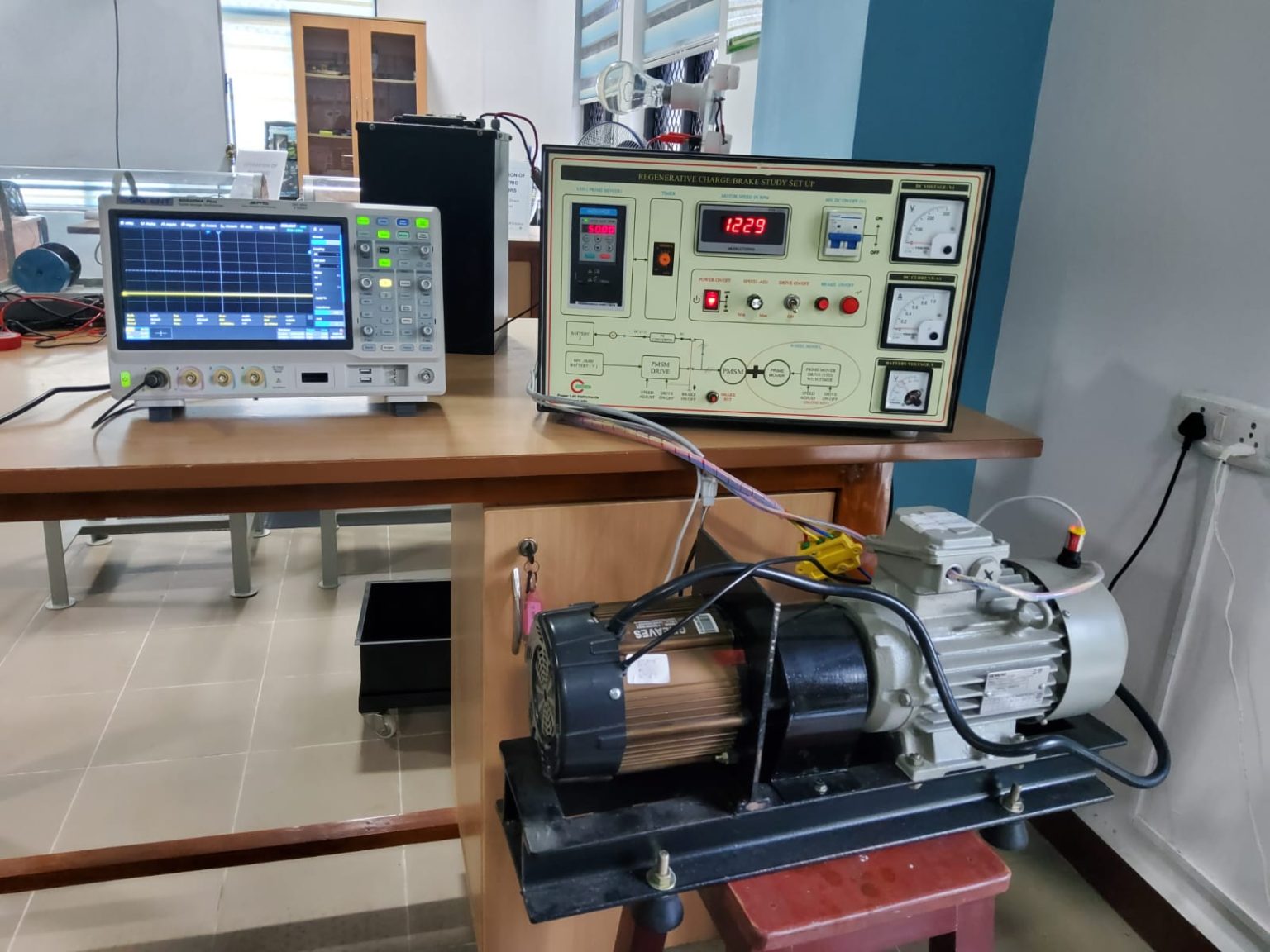
Address
ED 304, Department of Engineering Design,
IIT Madras
Phone
044 2257 5617
lead.emobility@coezet.iitm.ac.in